This is the first of a two-part blog series describing an incident involving conveying machinery that seriously injured a miner. Part 1 describes the machinery and the incident. In Part 2 I will summarize my engineering analysis of the incident and share the conclusions I reached.
A loaded, inclined conveyor belt may contain hazardous levels of energy due to gravity. To protect workers, anti-reverse devices called backstops are installed on inclined conveyors to prevent unexpected downhill movement. The Conveyor Equipment Manufacturer’s Association (CEMA) defines a backstop as:
A unidirectional mechanical device that allows the conveyor to operate only in the desired direction. It permits free rotation of the drive pulley in the forward direction but automatically prevents rotation of the drive pulley in the opposite direction. The backstop prevents the belt reversing and the material rolling back down an incline when the motor is non energized or other failures occur. Actuation is automatic and inherent to these mechanical devices to control such an issue.
A conveyor backstop is a safety device. Without a backstop installed, gravity can accelerate a loaded conveyor belt into a runaway condition. Serious injury or death may result. The ASME B20.1-2000 conveyor standard requires a backstop. It reads in part:
5.5 Backstops and Brakes
Anti runaway, brakes, or backstop devices shall be provided on all incline, decline or vertical conveyors where the effect of gravity will allow uncontrolled lowering of the load and where this load will cause a hazard to personnel.
Common designs for backstops include sprag and roller-style one-way clutches. Both devices work to prevent reverse motion by jamming a roller or a Figure-8 shaped sprag between inner and outer bearing races. A diagram of a one-way clutch is shown in Figure 1 below.
Literature concerning inclined conveyors often states that only one backstop is usually mounted to a belt pulley drive shaft. Recently I investigated an incident where two backstops were actually required. A miner was seriously injured by a runaway inclined conveyor loaded with many tons of stone.
On the day of the incident, the inclined conveyor transporting limestone out of the mine became overloaded. As a result, v-belts connecting electric motors to speed reducers on the north and south sides of the conveyor head pulley failed. The conveyor stopped and a single backstop mounted on one of the speed reducers kept the loaded belt from reversing due to gravity.
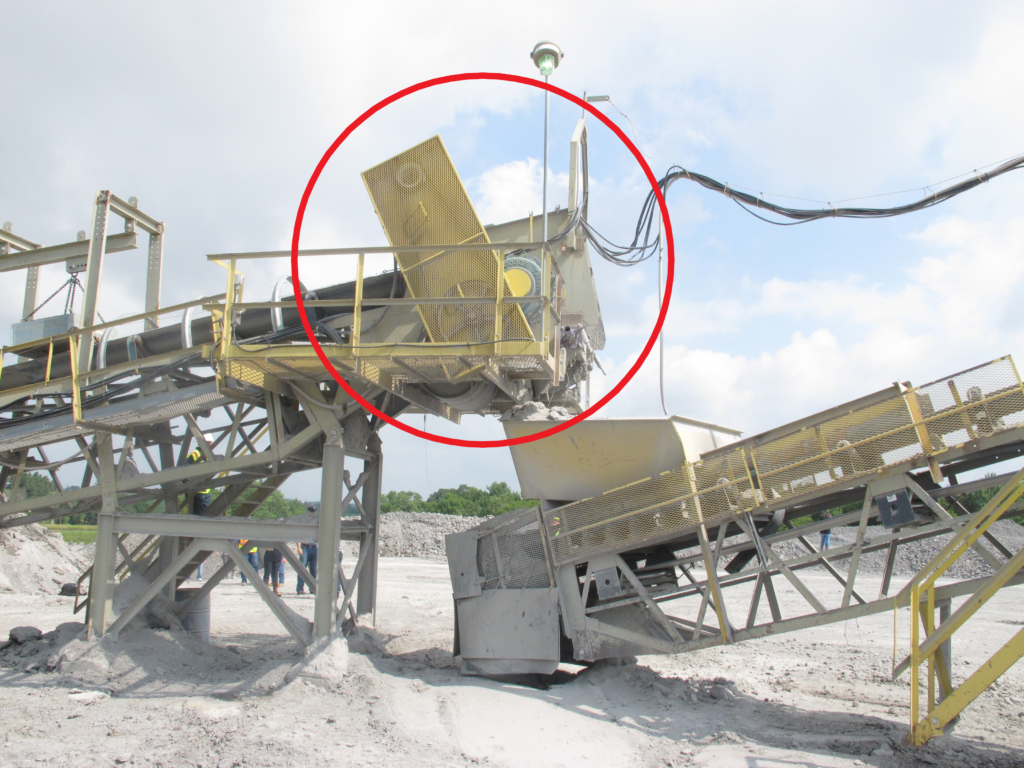
Figure 2: A view of the head pulley of the conveyor. The belts are behind the yellow expanded metal guard. The speed reducer is the rounded green object partially visible behind the belts.
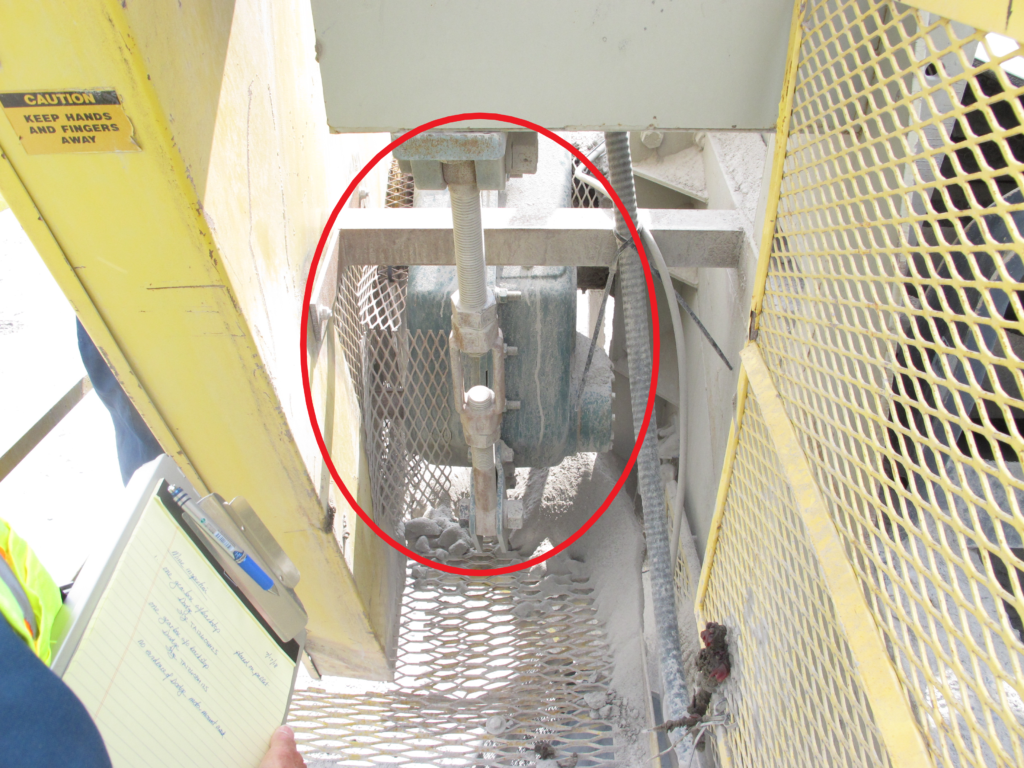
Figure 3: A view of a speed reducer and a torque arm with a turnbuckle. The purposes of the torque arm are to tension the v-belts and prevent movement of the speed reducer.
Four workers responded to replace the v-belts. To do so, they first loosened a turnbuckle on a torque arm connected to the south-side speed reducer. The conveyor did not move while the miners serviced the south side motor and replaced the belts because it was held by a single backstop mounted in the north side speed reducer. The miners replaced the belts and retightened the turnbuckle without incident.
The miners then attempted to replace the v-belts on the north side. They discovered that the turnbuckle on the north side torque arm was seized and the torque arm needed to be replaced. One miner held a wrench on the turnbuckle mounting plate nuts while another removed the bolts connecting the turnbuckle mounting plate to the conveyor frame. When the last bolt was removed, the conveyor belt and its heavy load of limestone suddenly reversed downhill. There was no backstop attached to the south side speed reducer. With the north side torque arm removed, there was nothing to hold the load and nothing to prevent the large, heavy north side speed reducer from rotating along with the head pulley as the load ran away downhill. The north side speed reducer repeatedly struck and severely injured the miner who had been holding the wrench until a coworker pulled him to safety.
In the second blog in this series, I will discuss my engineering analysis of the incident and the machinery involved and share the conclusions I reached.
Jeffery H. Warren, PhD, PE, CSP, is the chief engineer and CEO at Warren specializing in mechanical, machine design and safety. His deep expertise in machine design and safety analysis makes him a frequent presenter, trainer and expert witness. In addition to investigating more than 2000 claims involving property damage and injuries related to machinery and equipment since 1987, Jeff has an undergraduate degree in Mechanical Engineering from UNC Charlotte as well as a Master of Science and a Doctorate in Mechanical Engineering from Virginia Polytechnic Institute and State University — both with machine design emphasis.